Reactor Tanks: Exploring the Versatility and Functionality in Industrial Processes
Reactor tanks play a crucial role in various industrial processes, providing a reliable and versatile solution for chemical reactions, mixing, and storage. These tanks have become an integral part of many industries, such as pharmaceuticals, petrochemicals, and agriculture, due to their wide range of functionalities and the ability to handle diverse substances.
Facilitating Chemical Reactions
One of the primary purposes of reactor tanks is to facilitate chemical reactions. The tanks are designed to create controlled environments where reactions between different substances can occur under specific conditions. These reactions can involve various processes, including synthesis, fermentation, oxidation, and chlorination, among others. Reactor tanks allow researchers and scientists to carefully manipulate variables such as temperature, pressure, and mixing rate to optimize reaction conditions and ensure desirable outcomes.
Mixing and Blending Efficiency
Additionally, reactor tanks are instrumental in the mixing and blending of chemicals. The robust construction of these tanks allows them to handle high-pressure and high-temperature applications, making them ideal for achieving thorough and uniform mixing of substances. The tanks can accommodate different types of agitators, which help in breaking down solid particles, dispersing gases or liquids, and promoting homogeneity. This level of mixing efficiency is crucial in industries that require consistent quality and precise formulation of products, such as the pharmaceutical and food sectors.
Storage Functionality
Apart from facilitating chemical reactions and mixing, reactor tanks also serve as storage vessels. Many industries demand large quantities of raw materials or finished products, which need to be stored safely and efficiently. reactor tank provide a secure and stable environment for storing liquids, gases, and solids. These tanks are often equipped with additional features like insulation, heating or cooling jackets, and pressure relief valves, ensuring optimal storage conditions and minimizing the risks associated with the products being stored.
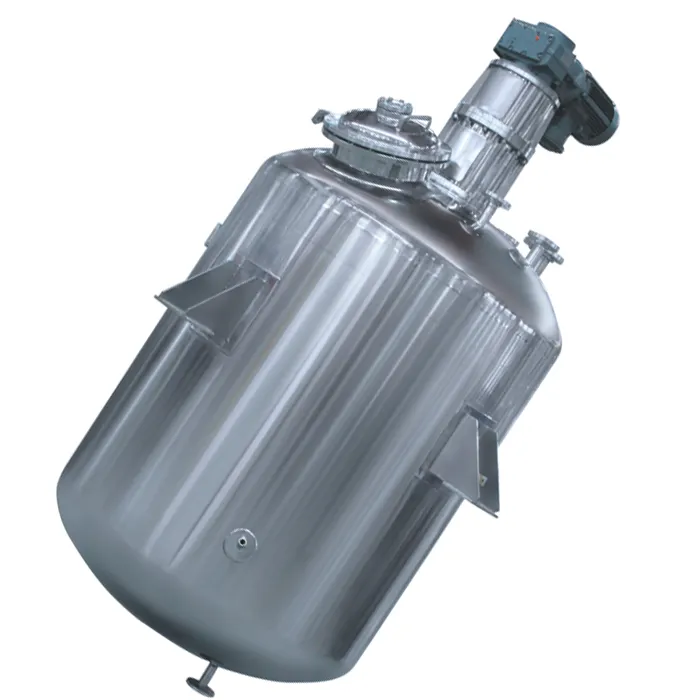
Customization and Material Options
The versatility of reactor tanks extends beyond their inherent functionalities. These tanks can be customized to suit specific process requirements, such as size, shape, and material. Depending on the industry and the substances being handled, reactor tanks can be fabricated from stainless steel, carbon steel, or even specialized alloys to withstand corrosive chemicals. Moreover, reactors can be designed with various configurations, including vertical or horizontal orientation, depending on space constraints and operational preferences.
Integration of Automation and Control Systems
In line with advancements in technology, modern reactor tanks often integrate sophisticated automation and control systems. These systems not only allow for real-time process monitoring but also ensure enhanced safety and efficiency. Automation enables operators to precisely regulate variables like temperature, pressure, and agitator speed, improving process control and reducing human error. Additionally, automation allows for remote monitoring and data acquisition, facilitating predictive maintenance and optimizing operational parameters.
Essential Solutions for Industrial Processes
Overall, reactor tanks offer an essential solution for a wide array of industrial processes. Their versatility, functionality, and customization options make them indispensable in industries that rely on chemical reactions, mixing, and storage. Whether it is the production of pharmaceuticals, polymers, petrochemicals, or agricultural products, reactor tanks provide the necessary tools and equipment for successful process optimization and consistent product quality. As industries continue to evolve and demand more efficient and innovative solutions, reactor tanks will likely remain a crucial element in driving industrial progress and success.